The principle of how an aircraft generates lift can be
explained by digging deep into some valid theories. But over the years false
theories have developed and as a consequence, it has mislead people on how an
aircraft actually generates lift. These theories are big nightmares for an Aerospace
Engineer.
First
False Theory - Longer Path Theory also known as the ‘Equal Transit Theory’.
This theory tells us that the aerofoils which are the
cross section of the wing are shaped with its upper surface longer than the
lower surface. So when the air strikes the leading edge it gets separated, and
the air molecules above needs to travel a longer distance compared to the air
molecules which are below.
This implies that the air molecules above must travel
faster than the air molecules below in order to meet at the trailing edge of
the wing. And from the Bernoulli’s Principle we know that faster velocity means
lower pressure and lower velocity means higher pressure provided there are no
gravitational effects.
This results in a lower pressure above and high
pressure below the aerofoil. This difference in pressure causes a net force
upward and guess what, that force is LIFT.
The reason why this is a false theory is because air
molecules above the aerofoil cannot just magically meet the air molecules below
the aerofoil at the trailing edge.
In fact studies suggest that the air molecules which
belong to the upper surface of the aerofoil leave the trailing edge way before
the air molecules which belong to the lower surface of the aerofoil.
Although the above theory is wrong, one thing is
surely valid that a difference in pressure is required for generating lift. To
create this pressure difference any one or both of these things should be met
i.e.
1. Aerofoil
should be cambered
2. Aerofoil
should be inclined at positive angle relative to flow direction.
The
Real Scenario
Viscosity which is the friction between adjacent
layers of fluid plays a crucial role in generating lift.
This viscosity leads to the formation of a starting
vortex which is nothing but a whirling mass of air in counter-clockwise
direction.
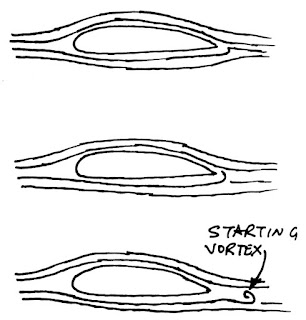 |
Formation of Starting Vortex
|
For conservation of the angular momentum, there is an equivalent
motion around the aerofoil in clockwise direction. This takes a form of what is
known as circulation around the aerofoil.
 |
Direction of Circulation and Starting Vortex
|
So when a vector addition of velocity vectors of this
circulation is performed on the freestream air velocity vectors, we get a
higher magnitude of velocity above the wing and lower magnitude of velocity
below the wing.
 |
Vector Addition of Freestream Air and Circulation resulting in high velocity above and low velocity below the aerofoil
|
From the Bernoulli’s Principle again, faster velocity
means lower pressure and lower velocity means higher pressure.
As a consequence the wing has low pressure on the
upper surface of aerofoil and a high pressure on the lower surface of the
aerofoil resulting in LIFT.
Second
False Theory – Skipping Stone Theory
This theory says that the Lift force is simply a
reaction force as a result of the air molecules striking the lower surface of
the aerofoil as it moves through the air. This case is similar to that of a
flat rock when thrown at a shallow angle across a body of water, hence the name
“Skipping Stone Theory”.
The reason why this is a false theory is because it
does not talk about what’s happening on the upper surface and only considers
the bottom surface.
The
Real Scenario
We know that lift is a force. From Newton’s second
law, force equals mass times acceleration and acceleration is defined as time
rate of change of velocity. So we see that force is responsible for change in
velocity and likewise a change in velocity generates a force.
Keeping this in mind, when both the surfaces of the aerofoil
deflect or turn the air, the local velocity of the air is changed in magnitude,
direction or both. The bottom surface deflects it or we can say the air bounces
of the wing and the upper surface bends the air around or we can say the air
sticks to the upper surface and is guided down by the Coanda Effect.
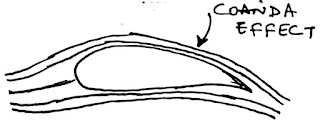 |
Air sticking to upper surface and guided down
|
Coanda Effect can be thought of as a love effect
between the air molecules and the surface. Air molecules have a tendency to
stay attached to the convex surface, in this case the upper surface of aerofoil.
So the combined effect is that the air pushes the aerofoil
up and back, which is nothing but Lift and Drag. This whole scenario can be
also thought as a result from Newton’s Third Law. This correct theory is known
as Newtonian theory of flow turning.
Why
two explanations for explaining how an aircraft generates lift?
Both the explanations are correct in their own way,
it’s just two different ways of looking at the same thing i.e. how an aircraft
generates lift.